What is Handloom and how to identify genuine handloom products?
Handwoven
The Loom
The Community
Handloom fabrics are created on a manually operated hand weaving device called a loom. The process involves entwining a set of vertical threads, the ‘warp”, with a set of horizontal threads, the ‘weft”.
The loom holds the warp threads under tension to facilitate the interweaving of the weft threads over and above the warp, using a weaving shuttle. Handloom weaving is a labor of love as much as it’s a source of livelihood for Indian artisans. It requires utmost patience, artistry, and technical skills, not to mention physical strength!
Handlooms have a direct connection to the culture and people of each community they come from. The motifs, patterns, and techniques are passed down in families from one generation to the other, and form an identity and cultural artifact.
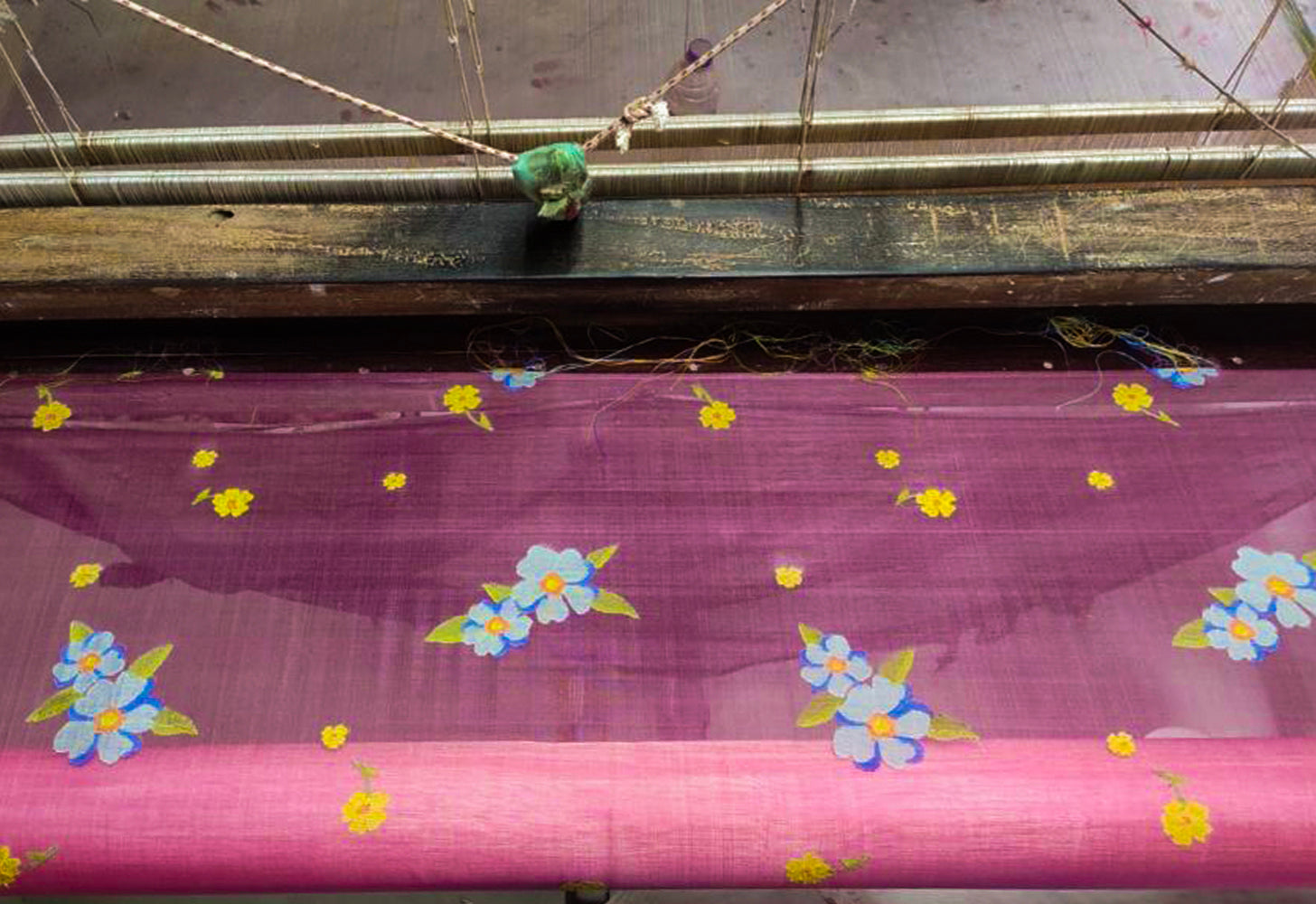
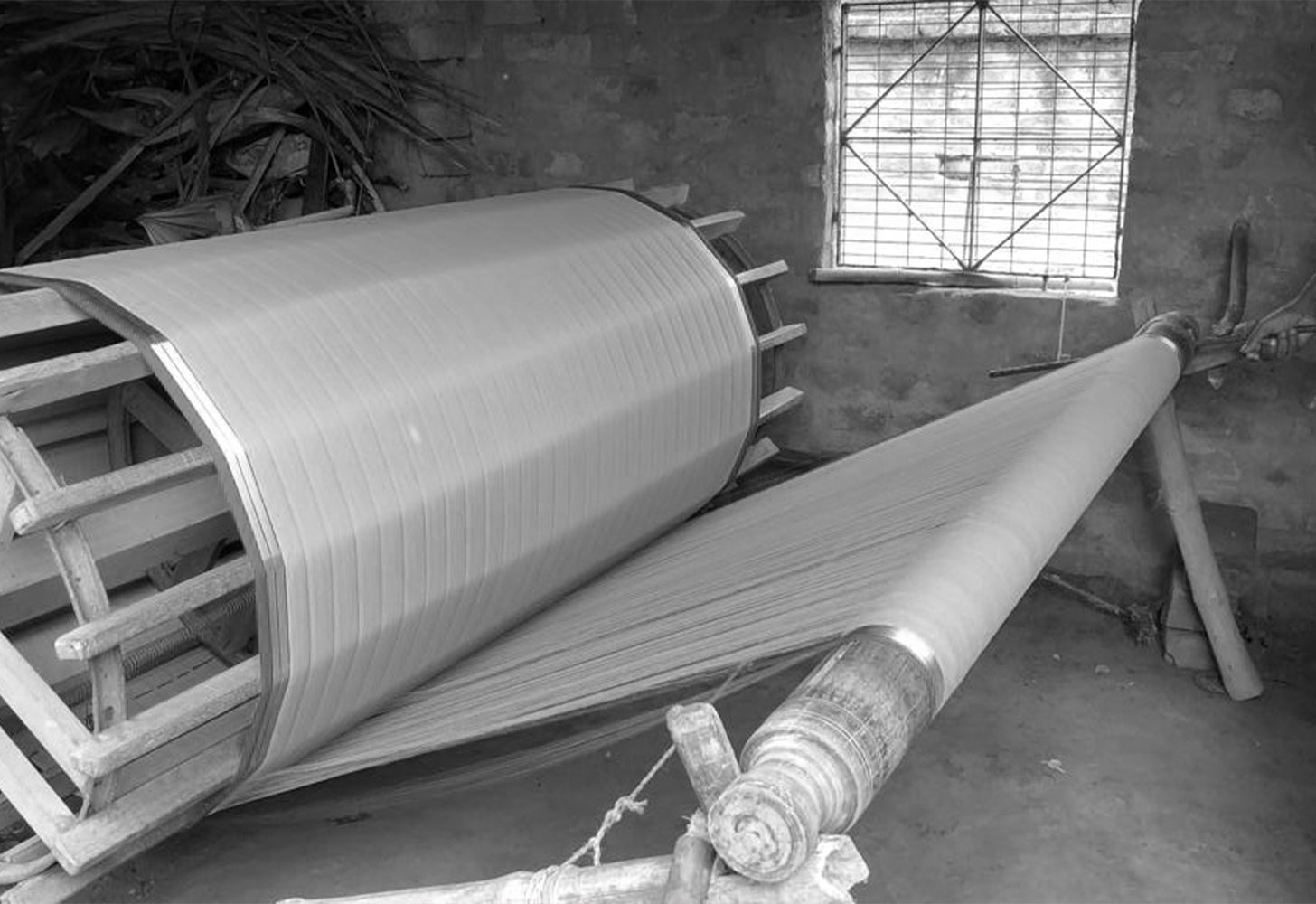
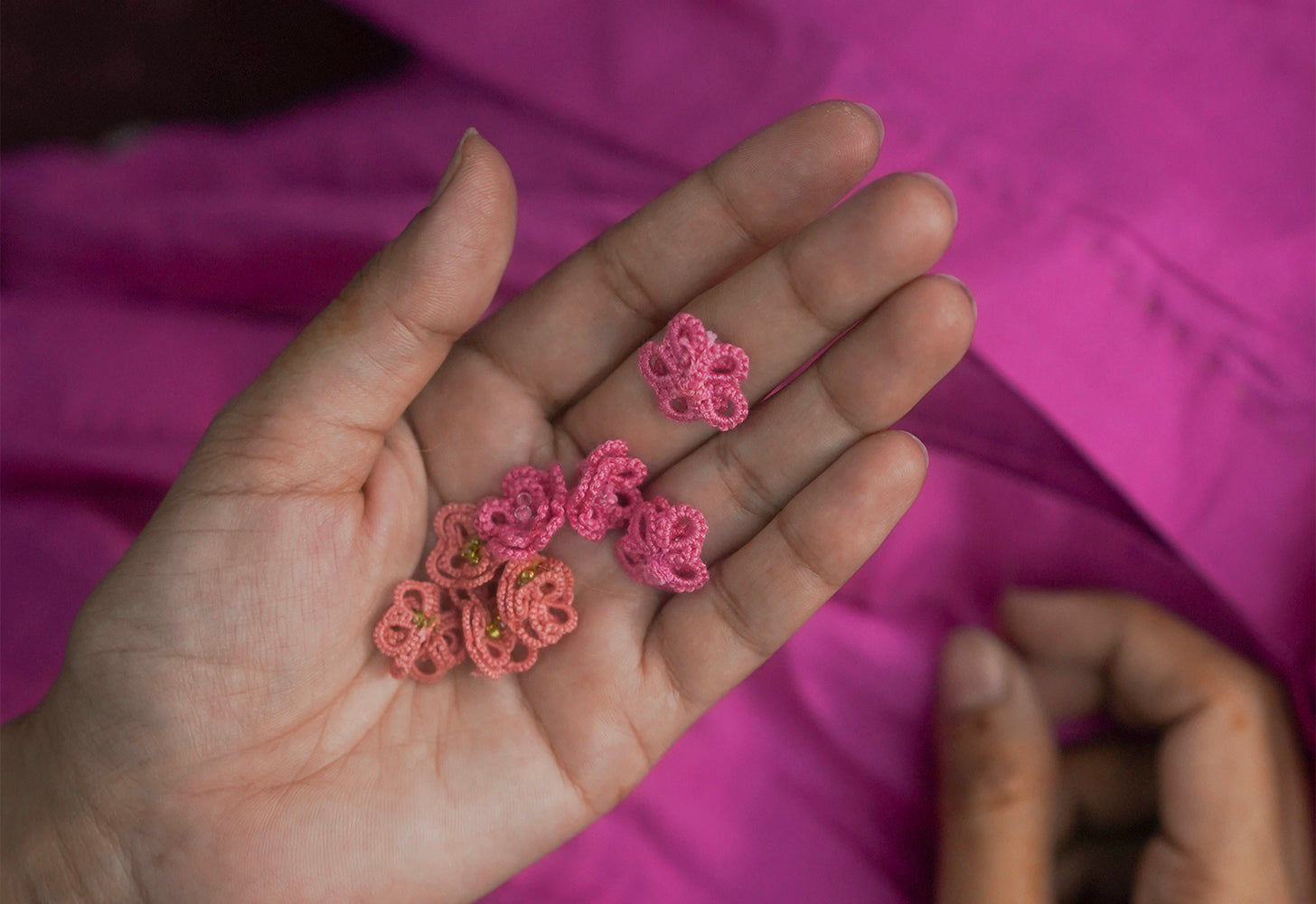
Why do we work with Handloom?
Hailing from a country with one of the richest and most diverse histories of textiles and techniques, our strong affinity for championing handloom products wasn't just a choice; it was deeply ingrained in us.
-
Uniqueness
Unique masterpieces reflecting the weaver's dedication, passion, and skill.
-
Creativity
Empower weavers with total control of the creative process, fostering new ideas.
-
Quality
Employ durable, natural fibers—cotton, linen, silk, wool—ensuring longevity.
-
Community
Fosters purpose, community, and preserves valuable traditions.
-
Source of Livelihood
Provides a source of livelihood for many rural communities, especially for women.
-
Comfort
More absorbent and breathable
-
Sustainable and Eco-Friendly
Epitomizes sustainability with natural, biodegradable fibers and re-use of excess material.
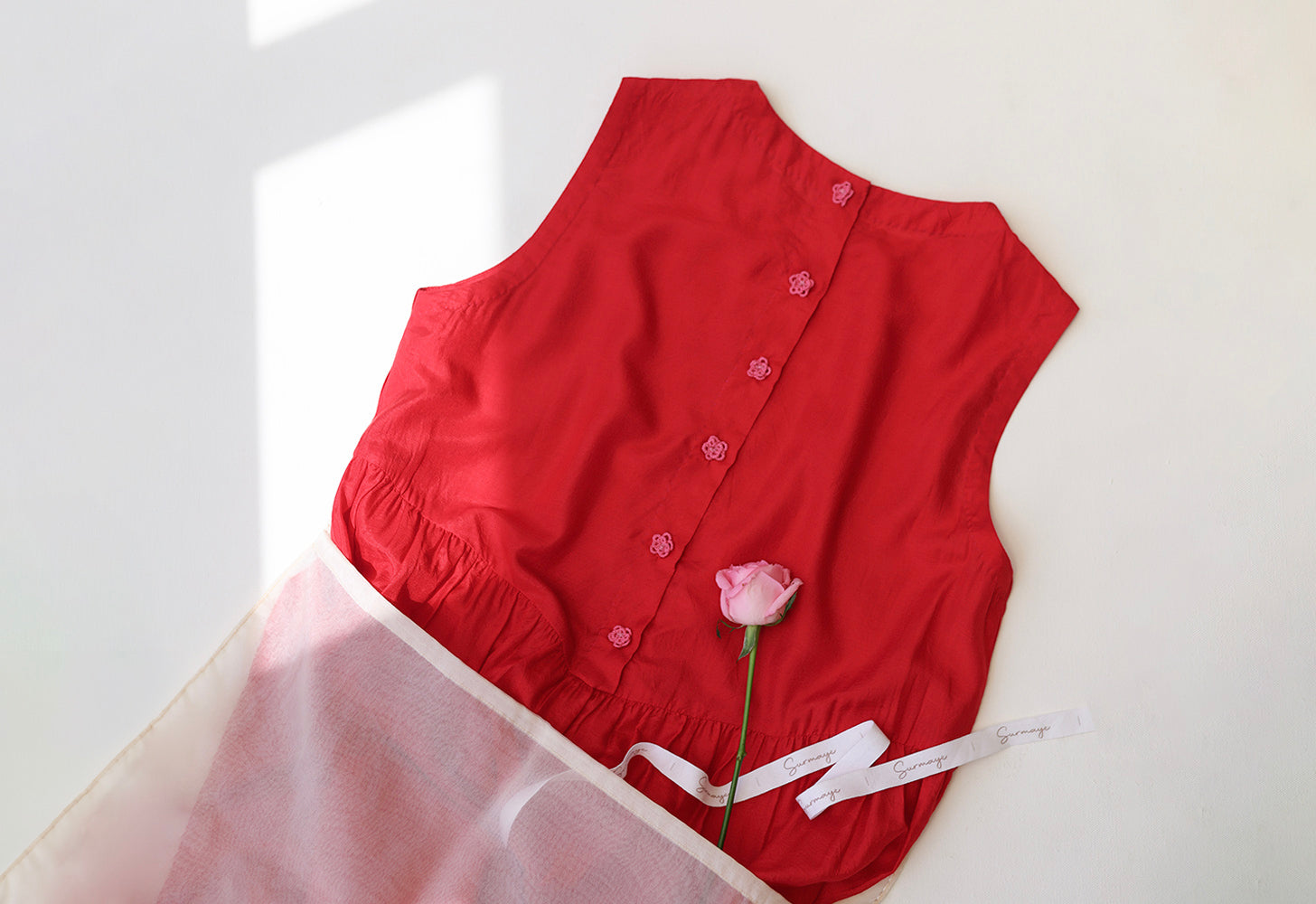
Why do we use Azo-free dyes?
We at Surmaye prefer to use Azo-free dyes that are better for you and the environment.
As Azo-free dyes do not consist of nitrogen-based compounds, they do not liberate amines which can be carcinogenic. They do not use heavy metals or harmful and toxic chemicals. Azo-free dyes also have a higher absorption rate, allowing for less water wastage in the dyeing process.
Azo dyes, on the other hand, have been found to be resistant to wastewater treatment, which means they can pass into the environment easily and cause harm.
Jamdani’s origins date back to the Mughal era — a time of opulence and refinement. The name Jamdani is derived from the Persian words Jam, meaning flower, and Dani, meaning vase. What sets Jamdani apart is the laborious and intricate weaving process. The process demands exceptional dexterity, patience, and an innate understanding of design.
After being set on the loom, a Jamdani saree can take anywhere from one week to one year to complete! The result is a fabric that appears almost weightless, yet boasts an astonishing complexity that captivates the eye.
Over time, different regions have contributed their own distinct flavor to the Jamdani weave. The Dhakai Jamdani, originating from Dhaka (Bangladesh), is renowned for its fine muslin base and intricate motifs. In India, the Nadia district varieties from West Bengal showcase Jamdani designs on silk, while Bardhaman specializes in cotton Jamdanis. Each regional variation adds a layer of cultural depth to this timeless art form.
At Surmaye, we work with weavers from the Nadia district in West Bengal, and our Jamdanis are handwoven using mulberry silk yarns.
The Process of Jamdani
-
I
Begins with calculating how much yarn is needed per color as per the design provided.
-
II
The required quantity of yarn is dyed using azo free dyes in the desired colors.
-
III
The dyed yarn is transferred to bobbins using the spinning wheel, which are later used for the warp and weft yarns.
-
IV
The preparation of the warp begins on a warping drum.
-
V
The yarns are transferred from the drum to the weaver’s beam.
-
VI
The denting is done where these warp yarns are pulled through the reed dent as per the reed plan.
-
VII
Now the loom is set, and the weaving can begin. Jamdani is woven on a simple pit loom.
-
VIII
Once the weaving is complete, the saree is removed from the loom and washed to remove any sizing or starch.
As you drape yourself in a Jamdani saree or garment, you don more than a piece of clothing – you become a bearer of a rich legacy, and a custodian of art that continues to weave the threads of history into the fabric of modern life.